Achieving a great deal more with a great deal less
- Oliver Novakovic
- Nov 2, 2018
- 3 min read
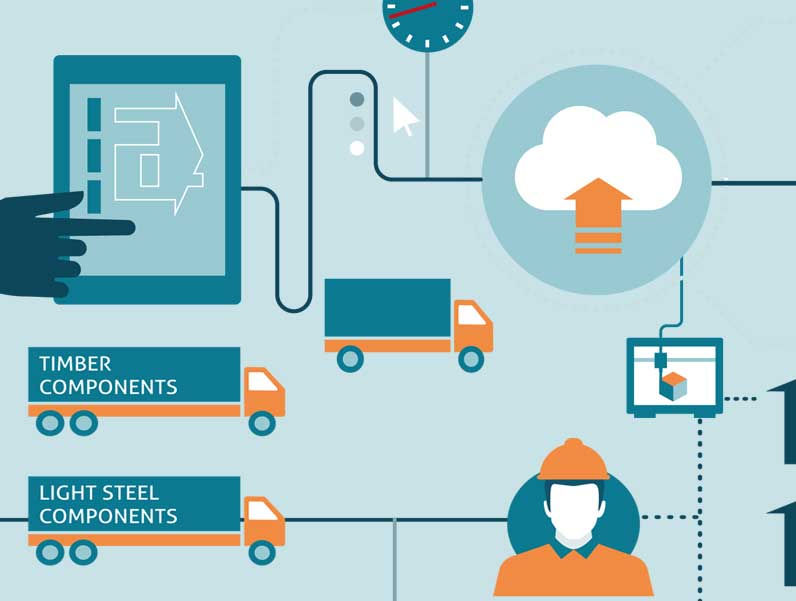
Last year Mark Farmer published a report into the UK’s construction labour model entitled ‘Modernise or Die’. He identified the need for innovation to solve the skills crisis, and claimed that “We have so big a challenge around the declining workforce in construction that we cannot recruit or retain our way out of it. We have to be prepared for a reducing workforce, which means we need to be able to build more with less”. That means new ways of building for the future.
As the UK’s largest house builder we’re putting considerable investment into modern methods of construction (MMC), including off-site manufacture, and in 2014 we set ourselves the target of having 20% of our housing output contain an element of off-site construction in it by 2020. Over a two-year period, we evaluated over 150 different suppliers and technology types. We are now trialling a variety of MMC, all of which will help us change our build profile in different ways. Whilst there are pros and cons to each of the systems, they all help us to reduce our reliance on particular trades, speed up build times, and improve safety on site, all while, when used at scale, maintaining efficient costs.
The most widely used of these is timber frame construction. Using timber frame can increase our build speed and change our labour demand profile. In particular, it changes the demand profile for bricklayers, enabling the existing bricklaying labour pool to operate more efficiently, so helping increase overall build volumes. Timber frame construction is actually one of the oldest methods of building a home, accounting for around a quarter of the homes being built in the UK, and is fully covered by the NHBC standards and mortgage providers. However, its use is extremely regional. Nearly every new home in Scotland is built with it, whereas in England its usage, while growing, is still much less common.
We are also looking closely at light gauge steel frame construction. We have recently finished a successful trial project in Southampton with Fusion Building Systems at our development in Swanbourne Park, where we constructed social housing properties using this method. We’re now rolling it out more widely, with four of our divisions trialling it across the South of England and in London. As Mike Fairey, Fusion’s director said, “The UK housing shortage is no secret and with building sites suffering a decline in available skilled workers, off-site construction is one way developers can ensure their build programmes deliver homes on time and on budget.”
The third main method we are actively trialling is large format block construction. Last year we hosted Secretary of State Sajid Javid at our site in Banbury for him to see the system, which consists of large format blocks that are 15 times larger than traditional blocks, with an integrated floor, wall and roof. The blocks create a watertight, inner-leaf shell using the same material as aircrete blocks, and are fixed using a thin mortar joint system. We are currently rolling this out across three of our divisions in the Midlands and Bristol, and just like the other two methods, it enables us to speed up construction whilst reducing the amount of labour needed to build the homes.
Despite the success of these methods, we have not stopped there. We recently hosted the ‘Barratt Innovation Challenge Sandpit’. A ‘Sandpit’ is a relatively new approach to supplier engagement that allows direct dialogue between our business and suppliers of exciting future technologies through a day of interactive workshops. The aim was to pool ideas for technology and process innovations that drive cost, quality and speed benefits whilst looking to use diverse skill sets. Among the ideas mooted were on-site safety solutions, alternative insulation applications and prefabricated masonry walling systems. At the end of the day we selected 5 products to be taken to an initial product review. One of these, an off-site flooring system from a company called Nu-Span, has already been installed on over 100 of our houses.
Our two key objectives when it comes to MMC are to future proof our housebuilding capability and to give our 27 divisions across the country options when they face either fluctuations in the regional availability of labour or materials. It is of course of vital importance that the new technologies used are fully assessed and reviewed to ensure they maintain the highest build quality standards. However, we feel that the benefits of these technologies are maximised when they complement, rather than replace, traditional construction methods. By investing in these modern methods of construction now we are hopefully making ourselves more resilient to deliver the high quality homes the country needs in the future. In the middle of a housing crisis where the industry is attacked for not building enough, that can only be a good thing.